Project
2,3-Butandiol and Maleic Acid from Hemicelluloses
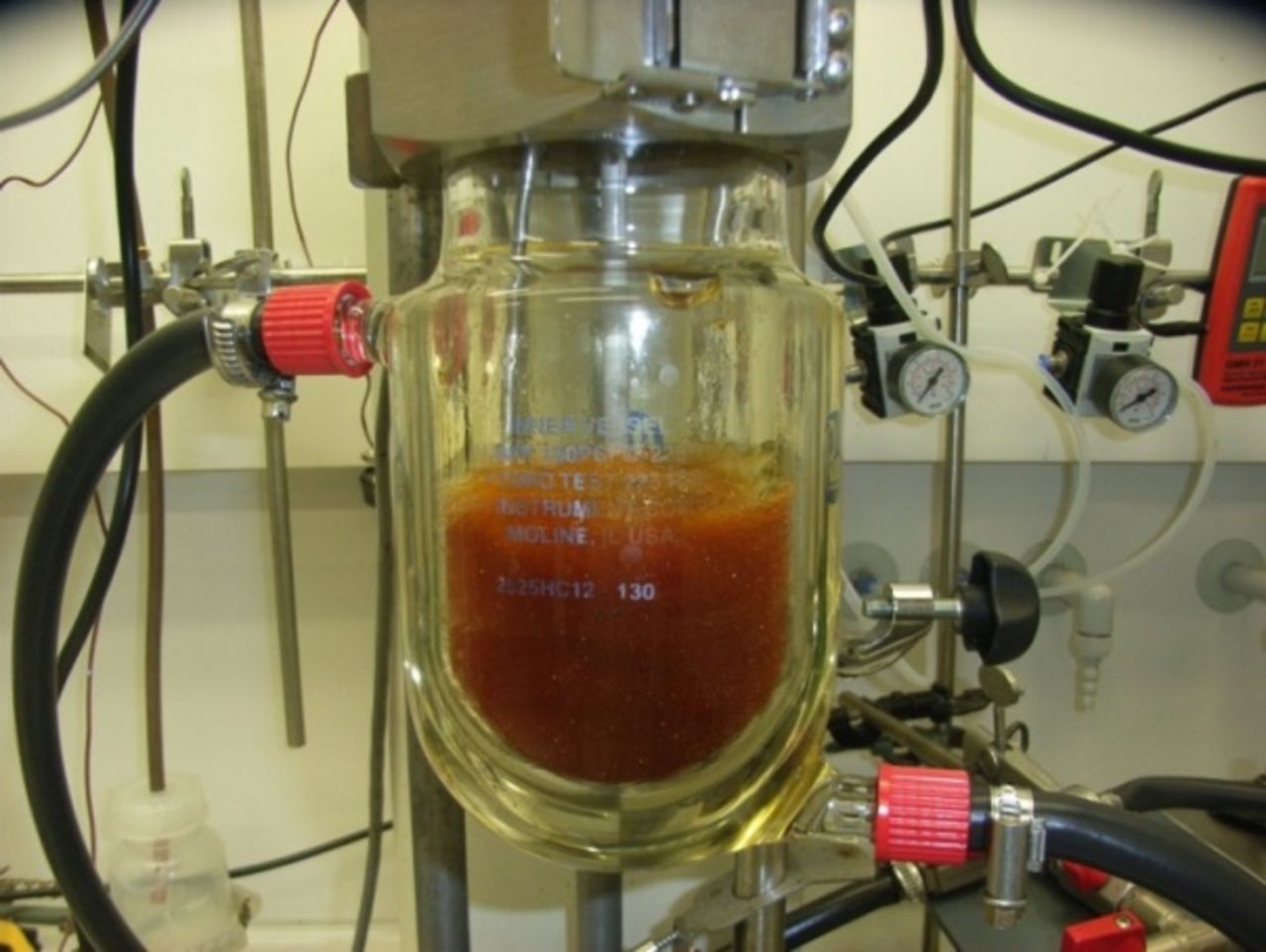
Controlled separation and conversion process for wood hemicelluloses
For a better utilization of biomass, the development of processes to convert hemicelluloses to value-added products is necessary. Exemplarily, we focus on the important industry chemicals 2,3-butanediol and maleic acid.
Background and Objective
The use of sustainable feedstocks plays an increasingly important role in industrial processes. Therefore, sustainable feedstock alternatives are needed that can replace fossil raw materials. Hemicelluloses as part of wood are available in large quantities. They do not compete with food production and, so far, they are only used in minor amounts in industry. The European joint project COSEPA will utilize the underused material hemicelluloses, starting with the separation and fractionation of wood to obtain pentoses for further refinement to different valuable products. The Thünen-Institute focusses on the development of a biotechnical process to produce 2,3-butanediol as well as the catalytic synthesis of furfural and maleic acid from pentoses. 2,3-butanediol is a possible bio-based feedstock for its further conversion to methyl ethyl ketone, currently used in quantities of 1.7 Mio tons/year for the production of paints and coatings. Furfural, maleic acid and maleic anhydride are important building blocks for polymers, e.g. resins. Its production amounts to nearly 2 Mio tons/year in sum. With the development of new process technologies based on hemicelluloses, noteworthy amounts of fossil feedstocks can be saved and important steps towards bio-based economy are made.
Approach
The biotechnological production of 2,3-butanediol is well known since the 20th century. The highest productivities and yields were achieved with the strains Klebsiella oxytoca and Klebsiella pneumoniae. However, as these strains belong to the pathogenic risk class 2 an industrial process using such microorganisms is hard to realize due to high cost for safety precautions. With risk class 1 microorganisms, such as Paenibacillus polymyxa and Bacillus licheniformis, it is also possible to achieve high yields of 2,3-butanediol using glucose as substrate. So far, there is only little information about the conversion of pentoses like xylose to 2,3-butanediol with these microorganisms and the yields that can be reached are rather poor. However, as processes based on pentoses as carbon source are far less optimized so far the prospects of reaching high amounts of 2,3-butanediol are promising.
In addition to the already known strains, a screening for new risk class 1 microorganisms capable to produce 2,3-butanediol will be carried out. The most promising strains will be further used for process optimization. In the end an efficient bioprocess for 2,3-butanediol production based on pentoses shall be established.
Currently maleic acid is produced by catalytic vapor phase oxidation of different petrochemicals (benzene, butane, butene) in only moderate selectivity. Likewise, the industrial furfural production processes features low yields. In the COSEPA project we want to produce furfural and maleic acid using pentoses instead of fossil raw materials. The challenge is to develop an effective overall process consisting of the subsequent reaction steps hemicellulose to pentoses to furfural to maleic acid.
Results
Several new risk class 1 microorganisms were discovered which are able to produce 2,3-butanediol in significant amounts. The new strains enlarge the possibility to find suitable ones for an efficient conversion of various feedstocks. Particularly interesting is the strain Bacillus vallismortis, which is capable to produce up to 79 g/l 2,3-butanediol + acetoin, the equilibrium product of 2,3-butanediol, from 180 g/l glucose in a batch fermentation. A yield of 0.43 g/g (theoretical yield is 0.5 g/g) can be achieved with a high productivity of 1.6 g/(l h) which is almost twice as high as with the so far best risk class 1 strain Bacillus licheniformis. In fed batch fermentation using xylose as substrate Bacillus vallismortis produces around 95 g/l 2,3-butanediol + acetoin in a yield of 0.49 g/g. This is the highest reported end concentration from xylose achieved with a risk class 1 microorganism. The same results can be achieved using acetate-reduced birch wood hemicellulose hydrolysates.
We were able to reach outstanding results in the acid-catalyzed conversion of xylose to furfural, which marks the first decisive step in the overall reaction sequence from hemicellulose to maleic acid, by applying hexafluoroisopropanol (HFIP) as in-situ extracting agent. Whereas the conversion of xylose to furfural is carried out in an acidic aqueous reaction phase, the formed furfural is extracted into the HFIP phase where it is protected from subsequent reaction lowering the yield. In contrast to the rather low yields of 30 – 55 % obtained in the current furfural production processes our new process leads to almost 100 % furfural yield. Further on, the reaction temperature can be lowered from 150 – 200 °C in the current processes to only 100 °C using our approach. Both the acidic aqueous reaction phase and the HFIP can be recycled and used several times.
The subsequent oxidation of furfural to maleic acid in a liquid phase turned out to be much less effective although various different reaction systems and catalysts were investigated. However, using our new furfural production process in combination with the gas phase furfural oxidation known since the 1930ies still offers a viable approach for the production of maleic acid from xylose in about 70 % overall yield.
Thünen-Contact
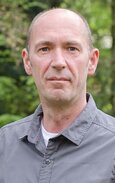
Involved Thünen-Partners
Involved external Thünen-Partners
-
Innventia
(Stockholm, Schweden) -
Lappeenranta University of Technology (LUT)
(Lappeenranta, Finnland) -
Edinburgh Napier University
(Edinburgh, Großbritannien (inkl. Nordirland)) -
Xylophane
(Bohus, Schweden) -
UPM Oyj, UPM NE Research Centre
(Lappeenranta, Finnland)
Duration
5.2014 - 4.2017
More Information
Project funding number: 22002314
Funding program: EU – ERA-NET WOODWISDOM +
Project status:
finished
Publications on the project
- 0
Kuenz A, Jäger M, Niemi H, Kallioinen M, Mänttäri M, Prüße U (2020) Conversion of Xylose from Birch Hemicellulose Hydrolysate to 2,3-Butanediol with Bacillus vallismortis. Fermentation 6(3):86, DOI:10.3390/fermentation6030086
- 1
Kallbach MK (2018) Biotechnische 2,3-Butandiol-Produktion aus Birkenholz-Hemicellulose. Braunschweig: Technische Univ, Fakultät für Lebenswissenschaften, 193 p, Braunschweig, Techn Univ, Fakultät für Lebenswissenschaften, Diss, 2018
- 2
Kallbach MK, Kuenz A, Prüße U, Staude C (2017) Schlussbericht zum Vorhaben : Thema: Kontrollierte Trenn- und Konversionsprozesse für Hemicellulosen ERA-WoodWisdom: "Controlled separation and conversion for wood hemicellulose (COSEPA)" ; Laufzeit: 01.05.2014 bis 30.04.2017. Braunschweig: Johann Heinrich von Thünen-Institut, 57 p
- 3
Kallbach MK, Horn S, Kuenz A, Prüße U (2017) Screening of novel bacteria for the 2,3-butanediol production. Appl Microbiol Biotechnol 101:1025-1033, DOI:10.1007/s00253-016-7849-1
- 4
Kallbach MK, Kuenz A, Prüße U (2016) Neuer Stamm zur biotechnischen Umsetzung von Xylose zu 2,3-Butandiol. Chemie Ingenieur Technik 88(9):1232